In the Belly of the Beast
17/02/18 22:16
The time has come. After months of design and documentation it is now time to manifest our ideas into reality. What that translates to is overcoming unforeseen obstacles. The Frozen Fury team had our sights set on 3-D printing most of the rover assembly, but when we received our resin we quickly realized that it required a secondary curing process that we had not anticipated. Suddenly a new project was added to our immediate list of things to do: assemble an oven with UV lights. The UND physics department was nice enough to donate one of their Cenco lab ovens to the cause. UV LEDs were soldered to panels that attached to the inner walls and we were ready to Rock 'n Roll.
As the rover parts printed and cured the next project at hand took focus. We wanted to construct to jig to stabilize align the fins to the fin can. The initial design was to fix fin stabilizers along a track that was affixed to the workspace at right angles. This allowed the tubing to be centered and held in place, fins attached, and held in place while the epoxy set on all 4 fins in one take. Jig Mk. I was operational and put to task on wooden fin dummies. Much to our chagrin the level of precision we desired did not meet satisfaction. After some brainstorming the team decided that the printer could be used not just for the rover but also to create the tools we desired. Jig Mk. II was modeled overnight and set to the printer the next morning.
Sixteen hours later…
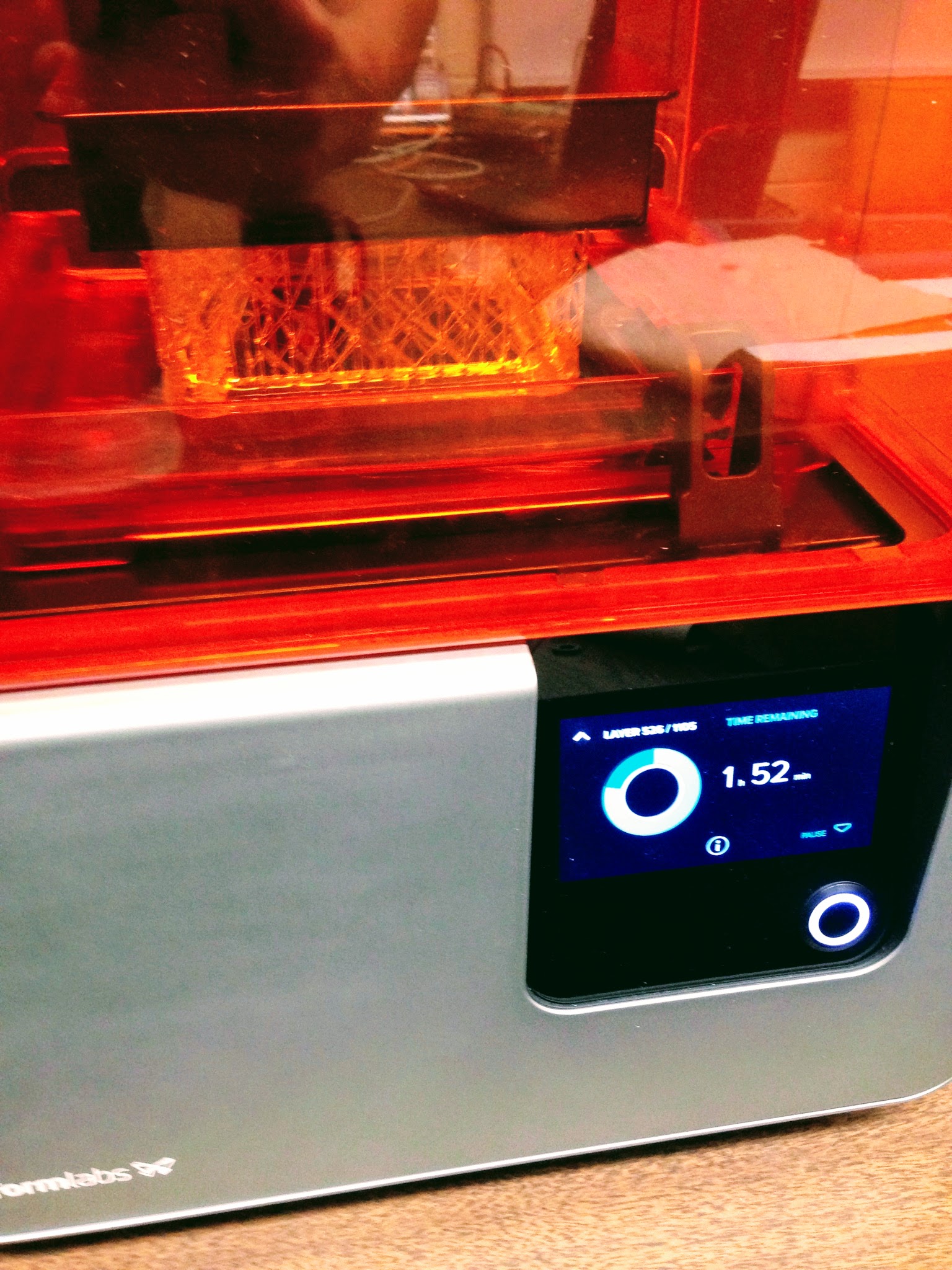
Part pyramid. Part sheath. All that we needed.
Jigs Mk. II were more like braces in essence and worked like a charm. All four fins held in place seamlessly and epoxied overnight. Now all we had left was to cut the side slits in the carbon fiber tube and sheath the motor casing core. The carbon tube was attached to the milling machine and straight lines cut in every ninety degrees.
After the first couple of weeks of finally getting hands on the materials and spending day after day in the machine shop it's certainly easy enough to say:
What a joy it is to be back in the belly of the beast.
As the rover parts printed and cured the next project at hand took focus. We wanted to construct to jig to stabilize align the fins to the fin can. The initial design was to fix fin stabilizers along a track that was affixed to the workspace at right angles. This allowed the tubing to be centered and held in place, fins attached, and held in place while the epoxy set on all 4 fins in one take. Jig Mk. I was operational and put to task on wooden fin dummies. Much to our chagrin the level of precision we desired did not meet satisfaction. After some brainstorming the team decided that the printer could be used not just for the rover but also to create the tools we desired. Jig Mk. II was modeled overnight and set to the printer the next morning.
Sixteen hours later…
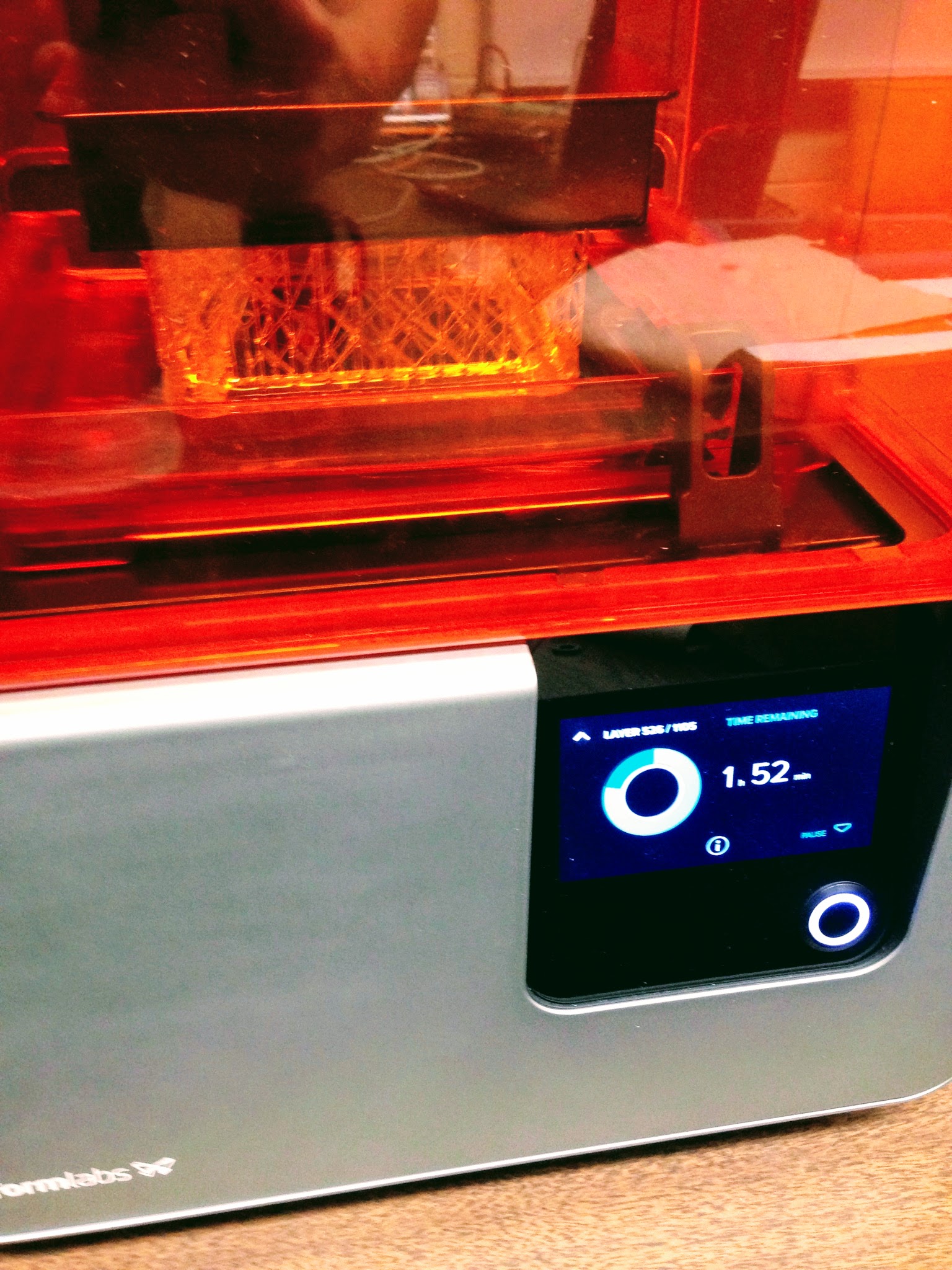
Part pyramid. Part sheath. All that we needed.
Jigs Mk. II were more like braces in essence and worked like a charm. All four fins held in place seamlessly and epoxied overnight. Now all we had left was to cut the side slits in the carbon fiber tube and sheath the motor casing core. The carbon tube was attached to the milling machine and straight lines cut in every ninety degrees.
After the first couple of weeks of finally getting hands on the materials and spending day after day in the machine shop it's certainly easy enough to say:
What a joy it is to be back in the belly of the beast.